Anodising
In modern manufacturing and product engineering, surface treatments play a crucial role in both aesthetics and function. Among the most reliable and versatile treatments is anodising, a process that strengthens, protects, and decorates metal components. At Frost Electroplating, our commitment to technical excellence and high-precision finishing makes us a trusted provider of anodising for industries where performance matters.
What Is Anodising?
Anodising is an electrochemical process that enhances the natural oxide layer on the surface of metal parts, particularly aluminium. Unlike coatings that sit on top of a substrate, anodising converts the metal’s surface itself, making it harder, more durable, and better suited for demanding applications.
The process creates a porous layer that can be left natural or sealed, dyed, or layered with further treatments. It improves wear resistance, corrosion protection, and even electrical insulation properties, making it ideal for use in both functional and decorative contexts.
The Science Behind the Process
The anodising process begins by immersing a metal component, most commonly aluminium, into an acid electrolyte bath. An electric current is passed through the bath, with the metal acting as the anode. This controlled oxidation thickens the metal’s surface oxide layer.
The thickness and characteristics of this oxide layer can be tailored depending on the voltage, electrolyte used, and duration of the treatment. Unlike paint or plating, the anodic layer won’t flake or peel. It becomes integral to the metal itself.
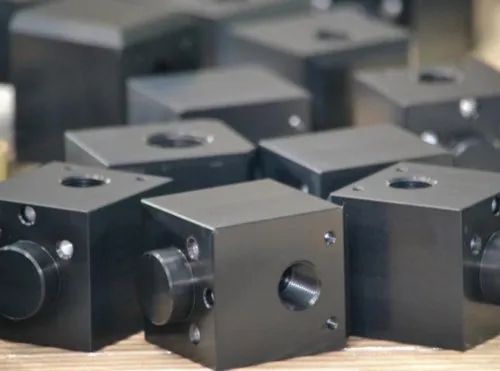
Common Types of Anodising
There are several types of anodising, each with distinct performance attributes:
β Type I - Chromic Acid Anodising:
A thin and less porous layer, ideal for parts requiring minimal dimensional change and good corrosion resistance.
β Type II - Sulphuric Acid Anodising:
This is the most common process, used for decorative and functional finishes. It allows for a variety of colours through dyeing and offers moderate hardness and corrosion resistance.
β Type III - Hard Anodising:
Also called hardcoat anodising, this method produces a very thick, dense oxide layer suitable for high-wear applications like aerospace or heavy machinery components.
Each method offers unique benefits depending on the environment and the function of the part.
Benefits of Anodising for Industrial Applications
The versatility of anodising makes it valuable across sectors. Its key advantages include:
- Durability: Enhanced surface hardness that resists wear and abrasion
- Corrosion Resistance: Ideal for parts exposed to harsh environments or chemicals
- Electrical Insulation: Acts as a non-conductive barrier where necessary
- Adhesion: Excellent base for painting or secondary coatings
- Aesthetic Appeal: Uniform colouring, matte or gloss options, and a premium appearance
These benefits make anodising a high-performance finish with lasting value.
Key Industries Using Anodised Coatings
Anodising is widely used in:
- Aerospace: For structural parts that require strength and corrosion resistance without added weight
- Electronics: Offering insulation and improving heat dissipation for enclosures and heat sinks
- Automotive: Enhancing durability and visual appeal in trims, housings, and suspension components
- Architecture: Providing weather-resistant finishes for cladding, railings, and handles
- Consumer Products: From cookware to mobile devices, anodising creates sleek and resilient surfaces
Frost Electroplating serves clients across all these sectors, tailoring the process to their exact needs.
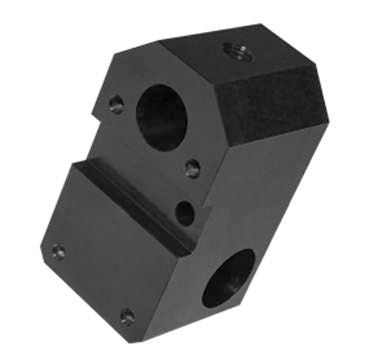
Anodising vs Other Surface Finishes
Unlike powder coating or electroplating, anodising does not apply material to the surface; it modifies the surface itself. This eliminates the risk of flaking or bubbling and retains fine detail in machined parts.
It’s also more environmentally friendly compared to some plating processes and offers superior longevity in high-wear conditions. While it may not provide the conductivity of silver or nickel, anodising excels in mechanical durability and corrosion control.
Design & Material Considerations
Before choosing anodising, it’s important to consider the base metal’s composition. Aluminium alloys respond differently to the process. High-silicon or high-copper alloys may not produce uniform results and may be better suited for other finishes.
Designers should also account for dimensional changes, especially with hard anodising, which adds thickness. Surface preparation, masking, and post-anodising treatments should all be factored in during early design stages.
At Frost Electroplating, we work directly with clients’ engineering teams to ensure precision, consistency, and compatibility.
Frost Electroplating’s Approach to Anodising
Frost Electroplating offers comprehensive anodising services tailored to high-spec industrial needs. Our facility is equipped with advanced bath controls, inspection tools, and custom finishing stations to handle both high-volume and prototype runs.
Our skilled technicians monitor every variable-bath chemistry, temperature, time, and voltage-to ensure optimal results. We provide full documentation and testing for aerospace and automotive compliance where required.
From consultation to delivery, we offer full transparency and support, making us a reliable partner for long-term metal finishing solutions.
Final Thoughts & How to Get Started
Anodising is more than a surface treatment-it’s a performance upgrade. Whether you need corrosion protection, electrical insulation, or aesthetic refinement, it delivers results that stand the test of time.
Frost Electroplating brings decades of experience, industry expertise, and quality assurance to every anodising project. If you’re ready to explore how this process can enhance your products, we invite you to get in touch.
Contact us today to learn more about our capabilities or request a tailored quote for your next project.